HE-Parts
Mining Profits with Lean
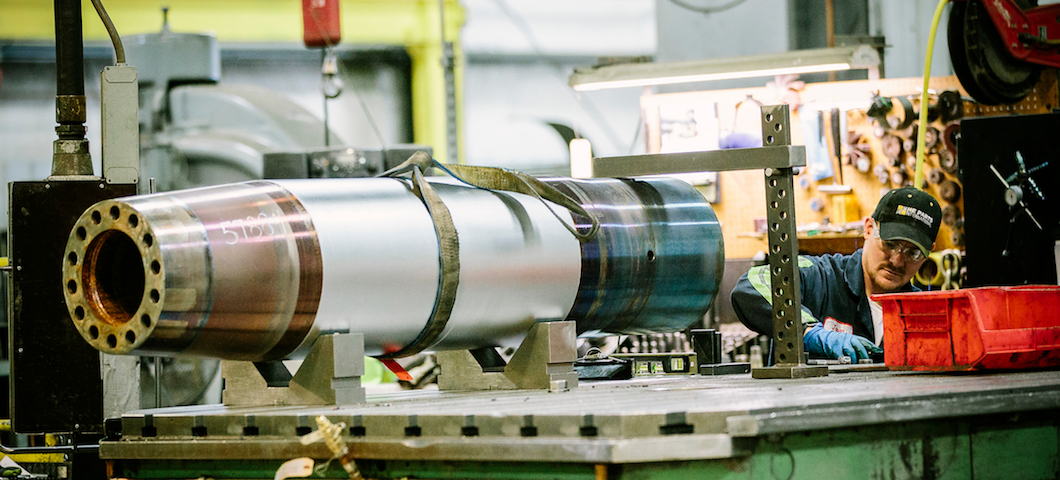
About H-E Parts International
H-E Parts International is a leading independent supplier of parts, remanufactured components, and equipment to the global mining, quarrying, heavy construction, and energy sectors. The atlanta-based company has a Mining Solutions devision in Billings, Montana, with a team of over 70 employees. The Mining Solutions technicians rebuild warn-out mechanical, hydraulic, and other components for a variety of mining trucks, some capable of carrying up to four hundred tonds of ore.
The Challenge
Due to the size and weight of the products and components, simply moving a part across the Mining Solutions facility can take a lot of effort. "This is about 18,000 pounds," said Shane Pence, the company's North American Strategic Projects manager, as he stood next to a seven-foot-tall wheel unit in June. That's one reason why Pence and other H-E Parts leaders sought help from the Montana Manufacturing Extension Center (MMEC), part of the MEP National Network, to improve flow and productivity and create a safer workplace.
MEP Center's Role
After listneing to their needs, MMEC's Senior Business Advisor Alistair Stewart hosted an eight-hour class for H-E Parts on Lean Manufacturing, a conceptual framework for Improving efficiency. Afterward, Pence and eight other H-E Parts employees decided to attend a 10-week course taught by Stewart as part of the Society of Manufacturing Engineers' Lean Bronze Program, in which participants apply the principles of Lean Manufacturing to their own businesses. The course helped H-E Parts to inventory its processes, find the ones that add value, and cut out the rest. The company made changes to its production facility area layouts in order to streamline WIP (work in process), and improved its machining, welding, and mechanical practices to eliminate unnecessary work. It also invested in some equipment upgrades. “We’ve made those (investments) back ten-fold in a month,” said Mike T.K. Hall, who supervises the crews that use CNC machines to restore old parts as well as produce new ones. The machinists like the new system, too, because their work flows more naturally. The Mining Services division now has the capacity to move more product with the same number of people, which has boosted morale. “It’s an inspirational story,” Stewart said. “Lean is all about engaging people, and once engaged, they are unstoppable.”
"The Return on Investment for us has been tremendous, and we're continuing to partner with MMEC to improve our overall competitiveness and ensure long-term success."
Shane Pence, North American Strategic Projects Manager